Manufacturing technologies with Berrang.
Together with you, we create the fastener solution that best suits your requirements - regardless of manufacturing technology or manufacturing process.
Fastener technology in perfection – for every requirement we offer an economically & technologically suitable manufacturing process.
We think your fastener from the solution. We are not dependent on our own production and not only know the manufacturing processes used there – often the general situation for many producers.
What this means for you: We decide together with you which economic and technological solution is best for you. In doing so, we rely on an open technology approach in which we select from a large pool of manufacturing processes to realize the right combination for you.
We decide on a case-by-case basis whether we can help you with standard parts or whether the development of an individual component would make more sense for you. In doing so, we work independently and can also offer a combinations of different manufacturing processes.
An overview of our manufacturing processes & surface technology:
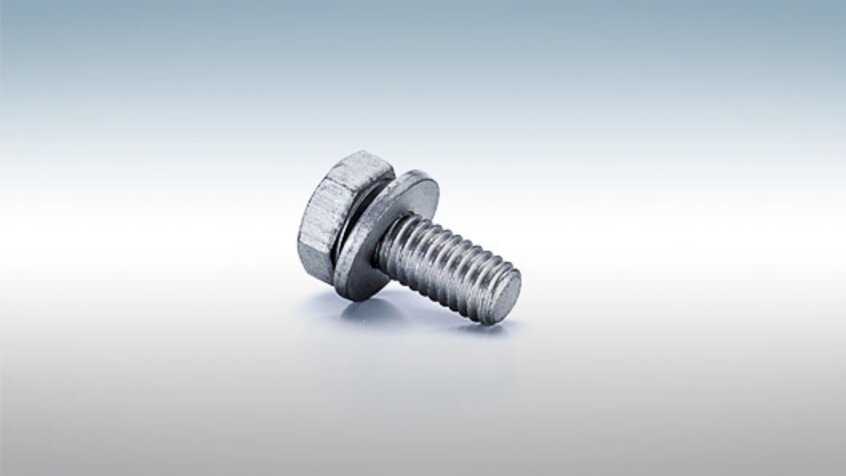
cold forging.
Cold forging belongs to the family of non-machining processes. It is forming process that usually produces both hollow and solid parts through a multi-stage manufacturing process.
The advantages at a glance:
- Production of complex components possible
- High volume output
- High dimensional accuracy
- Lower material consumption
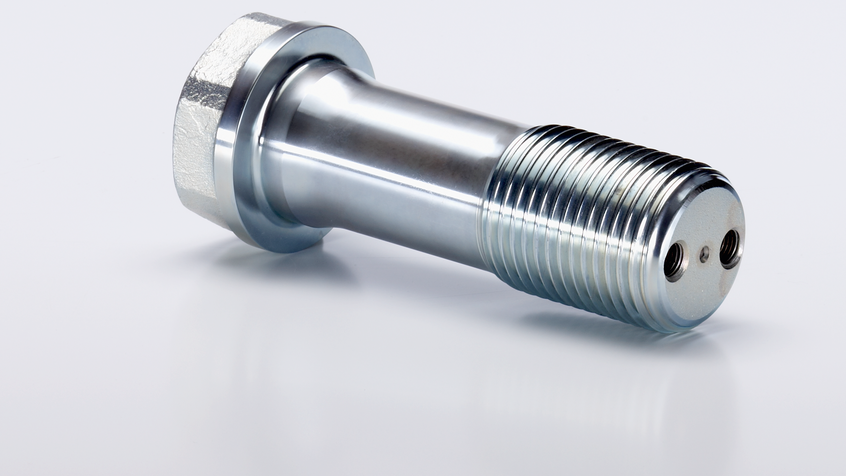
hot forging.
Hot forging refers to all those forming steps that take place at temperatures above the recrystallization temperature of a metal. The hardening that takes place during forming is cancelled out by recovery and softening processes that occur during and after the forming step. As a result, very high degrees of forming can be achieved, although dimensional tolerances and surface finishes are no as tight as with cold forming.
The advantages at a glance:
- Production of complex as well as very large components possible
- High durability of the parts
- Low amount of waste
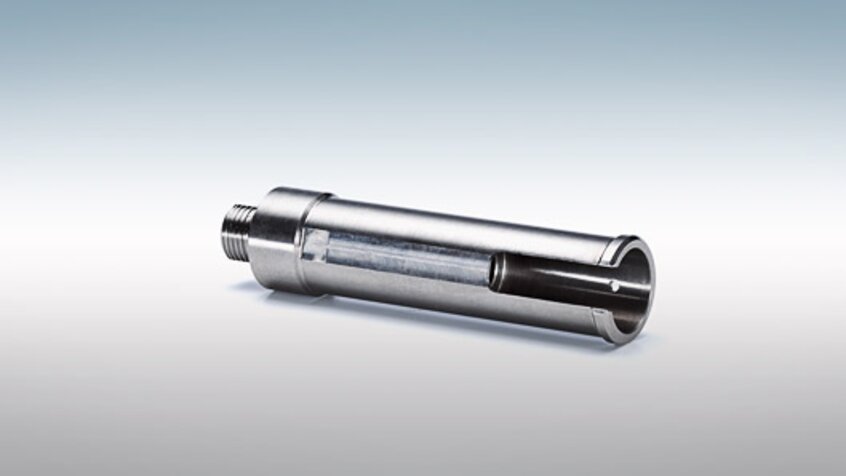
machining technologies.
Machining and cutting processes include threading, reaming, slotting, turning, milling, drilling, lapping, planing, honing, broaching and grinding. On the one hand, these metal-cutting processes allow more complex geometries with tighter-tolerance shapes to be achieved than with non-cutting forming processes.
The advantages at a glance:
- Low tooling and setup costs
- Production of small quantities economically possible
- High accuracy and tolerances
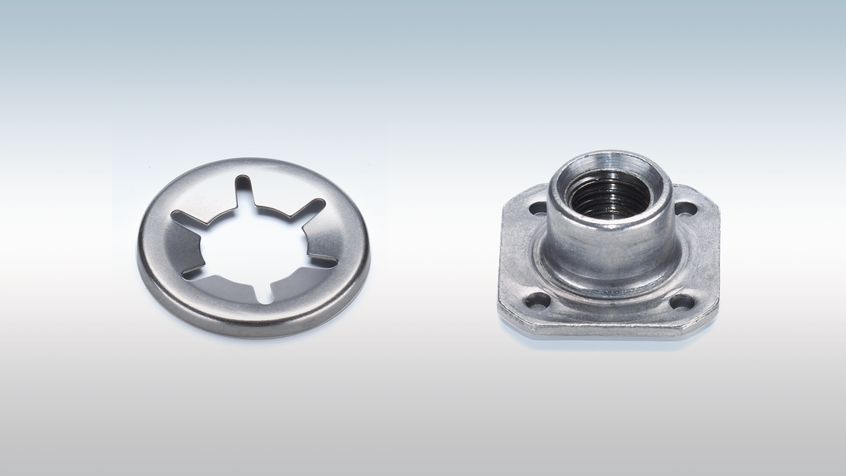
Deep drawing technology. Sheet metal bending technology. Stamping technology. Cutting technology..
Deep drawing is the tensile pressure forming of a sheet metal blank into a hollow body open on one side. For the production of complex sheet metal parts, a combination of these manufacturing processes is often used in progressive dies including sheet metal bending.
In punching, parts are made from sheet metal of a wide variety of materials using a press or impact and a cutting tool.
Laser cutting, also known as laser beam cutting, is a thermal cutting process for plate-shaped material and three-dimensional bodies (e.g. tubes or profiles) using a laser.
The advantages at a glance:
- Can be used economically even for very small batch sizes
- Complex geometries
- Precise & fast processing
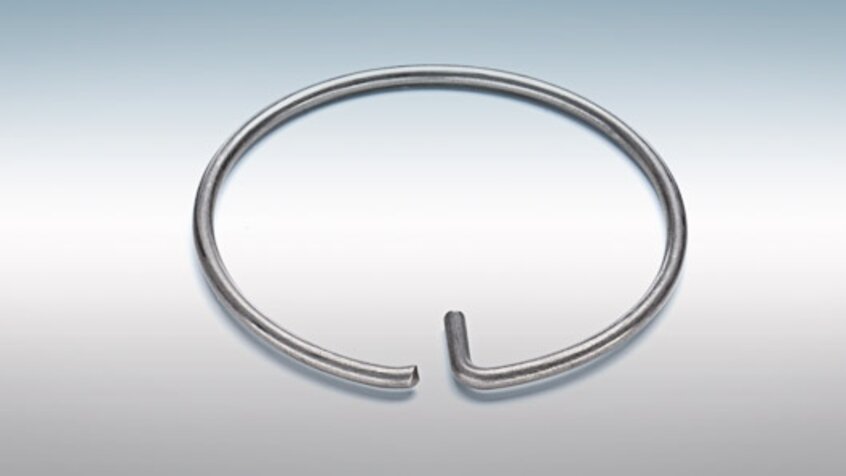
Wire bending technology.
Wire bending technology can be used to manufacture products from both round wire and profiled wire. A large part of technical springs also belongs to wire bending parts.
The advantages at a glance:
- High cost efficiency
- Can be used for many shapes and sizes
- High accuracy and tolerance
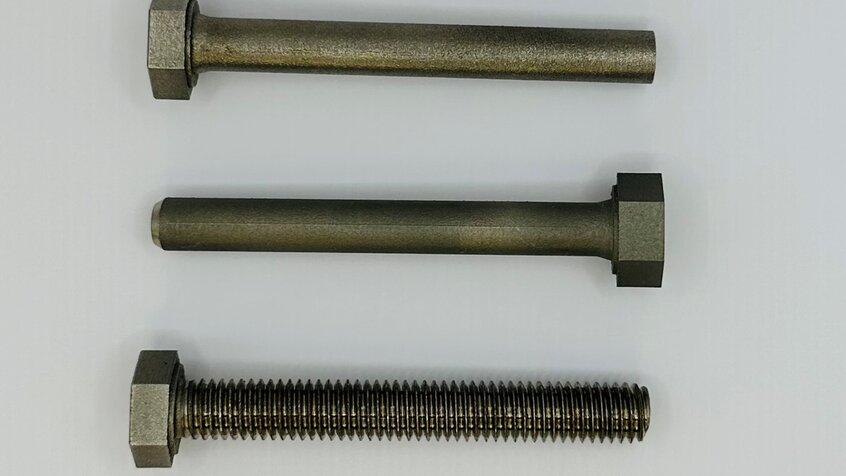
Additive Manufacturing.
3-D-printing is becoming increasingly important – and this is also true in the industrial sector. For this reason, we too are focusing on additive manufacturing.
Additive manufacturing technology has a profound impact on modern production, regardless of the materials used. The method allows raw materials to be applied layer by layer, ultimately creating complex, three-dimensional objects. The basic principles of this technology are relatively simple: an energy source is used to melt or sinter metal powders, and then layers are built up additively to form the desired workpiece. Currently, the most important processes in practice are selective laser sintering (SLS), selective laser melting (SLM) and laser cladding (LMD). Other processes include extrusion-based processes and nano particle jetting.
The special feature: The manufacturing process is based on a 3-D printer and 3-D CAD data, so no tooling is required. The process is mainly used for parts with a high degree of customization or for fasteners with a complicated geometry.
The advantages at a glance:
- Design freedom
- High functionality
- Time savings
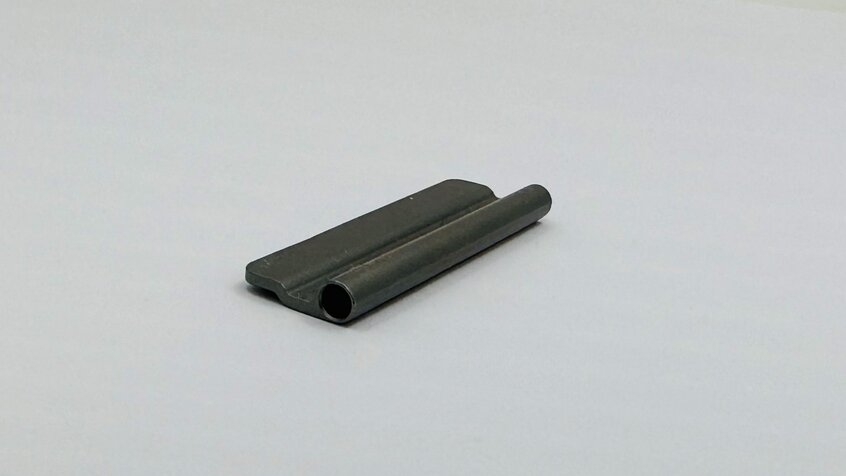
Metall-Injection-Molding.
The metal injection molding process, also known as MIM, combines two technologies: injection molding (known from plastic injection molding) and sintering technology. In this manufacturing process, fine metal powder and thermoplastic polymer resin are mixed to produce an injectable granulate that is injected into molds. It is used where complex as well as multilayer component geometries are desired.
The advantages at a glance:
- High strength & hardness
- Time saving
- Wide range of shaping options
- Use of medium and large quantities
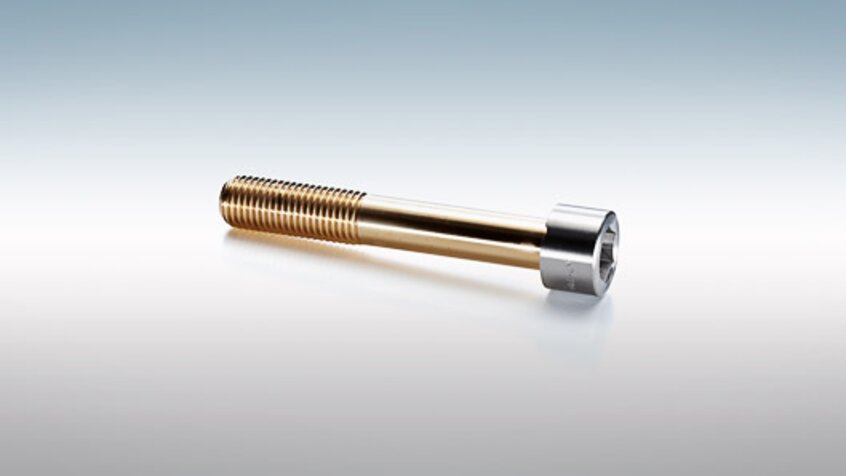
surface technology.
Coating systems today have to meet a wide range of requirements. In addition to the right manufacturing process for your component, we make sure that the surface technology also fits your solution. For example, they must protect against abrasion or corrosion, improve electrical conductivity or prevent sticking, but also serve decorative purposes. Often, there is also a combination of requirements to be met on the same product. We bring these properties together and monitor the processes in the respective supply chain.